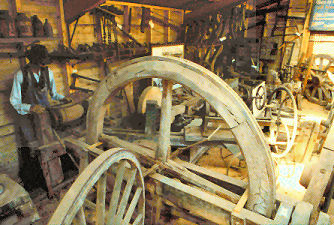
The Wheelwright's craft is amongst the oldest known to man, with the origins of the wheel dating back to prehistoric times. It was
probably Stone Age man who first realised that a rolling stone or a round log of wood moved more easily than an object, which needed
pulling or pushing. The first wheels were simply solid discs, carved out of one lump of wood, with solid wheels made from three shaped
planks following dating from about 5000 BC. Solid wheels were not only heavy, but also tended to break across the grain of the wood, and
so an improved and lighter wheel became desirable. By around 2000 BC, spoked wheels had begun to appear in Asia Minor, with the rims of
these early spoked wheels made from one or two pieces of wood bent to a full circle. The rim itself connected to the hub, known to
wheelwrights as the nave or stock, by wooden spokes. As the Iron Age proceeded, so the wheel developed, with tyres and nave bonds being
introduced, and by the Roman period, many wheels were very much as the Victorians were making them, with sectional felloes and one-piece
tyres. It was also about this time that the one-piece hoop tyre seems to have disappeared, only to re-emerge in the 18th century. Wheel
construction in the period before the 18th century used short strips of iron, called strakes (or sometimes shoes), nailed across the
joints of the felloes, and these wheels were known as 'being shod'.
Wheelwrights, apart from the use of differing materials, have been making wheels in the same way made since the early seventeenth
century. The only significant design change being the development of the 'dished wheel', which was shaped like a saucer and having the
hollow side facing outwards. With the spokes driven into the nave at an angle, so that the lowest spoke stood perpendicularly to the load,
the upper part of the wheel was sloping away from the body of the cart or carriage. This produced two distinct advantages. Firstly, it
enabled the body of the vehicle to be wider at the top than at the floor, and secondly it helped the wheel withstand the lateral thrust of
the axle caused by the action of the horse.
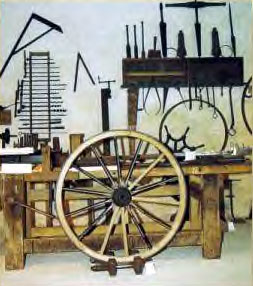
They were clearly Craftsmen of the very highest order, possessing as they did a great knowledge of the properties of timber, and the
acquired knowledge of their craft passed from father to son, and from master to apprentice. Before he could begin to practice his craft,
the wheelwright had to obtain his supply of timber, oak obtained locally during late spring and early summer, and ash, beech and elm during
the winter. The Timber would remain uncut until winter, when, using saw cuts marked out by the wheelwright, it would be cut and then left
to season for another five or six years before finally reaching the work bench in the form of sawn timber.
The construction of a Wagon followed traditional patterns and could be a lengthy process, with anything up to six months being normal,
different woods were used for the various parts of the wagon, the common factor being that all of the timber had been well seasoned for
many years before construction ever began. The wheelwright followed patterns for felloes, for the bottom timbers of a wagon, for a dung
cart, and for a raved cart. Raves being side rails added to a cart or wagon to allow for the carriage of a bigger load over the wheels.
There were also traditional patterns for wagon shafts, cart shafts, tail-board rails; indeed for every part of a cart, wagon, timber
carriage and other vehicles, for these were all part of the wheelwrights trade.
Making a Wheel
The wheel began with the nave or hub, originally rough-hewn with an axe, but later turned on a lathe. Elm was the wood of choice having
strong cross-grained fibres, which would not allow it to split when under strain. The hub made, the blacksmith (who always worked closely
with the wheelwright) would attach iron bands to give it added strength. These bands would be driven on red hot, and then plunged into
cold water for shrinking. The wheelwright would then marked out the places where the spokes were to be morticed into the nave, then used
a brace and bit to cut the holes, and chiselled them out using a 'buzz'. The spokes of oak were then shaped by axe, saw and spoke shave
to have the maximum of strength with the minimum of weight, then driven into the nave with a sledgehammer, not straight, but at an angle
to give the right amount of dish. The wheel spokes were fashioned with a drawknife and a spoke shave, and then driven home with a massive
hammer. The ends of the spokes were then marked off for the shoulders and tongues, which would fit into the felloes, usually made of ash,
elm, oak or beech, and cut out with a bandsaw, which were curved to take two spokes each.
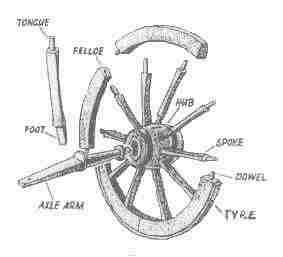
They were also bored to take the dowel of the adjacent felloe. The final procedure was the fitting of iron hoops (strakes) round the
circumference of the wheel. This was again the work of the blacksmith. It was a skilled operation and he had to ensure that the fit was
neither too loose nor too tight and only years of experience would result in a job well done. For shoeing, the wheel was then set up over
a pit of water. The wheelwright took out the strip of iron, already curved by heat and punched with nail-holes, and laid it red hot on
top of the wheel rim. As the hot iron burned into the wood, the wheelwright punched in big rose headed nails, and then turned the wheel
round into the pit of water. While the newly fastened strake was cooling, the same operation was repeated on the opposite side of the
wheel, until the six strakes completed the job of tyring. Shoeing a wheel in this manner continued until the latter part of the nineteenth
century.
Hoop tyres did not arrive in Britain until the last quarter of the eighteenth century, when solid bars of iron bent into
a full circle and welded, were put on hot and nailed into position on the wheel rim. As the tyre cooled and shrank, it pulled
the spokes into exactly the right amount of 'dish'. The nave bonds were heated, and then driven into place on each side of
the spokes, and finally, the wheel had to be boxed. This meant that the centre of the nave had to be hollowed out and a cast
iron box inserted and fixed with wedges. Into this box, the axle arm was fitted. Under the first Bylaws of the Worshipful
Company, it was a punishable offence to sell wheels before they had been boxed and shod. For most wheelwrights however,
wheels were only part of their work. They often built the cart or wagon, complete with shafts and axle-beds; it would be
their responsibility to see that the wheels hung properly from the axle-arms. The iron axle-arms had a slight downward and
forward slope, so that in a dished wheel the lowest spoke, which was at that moment taking the full weight of the load,
stood perpendicular.
The wheelwright's axe (an adze) had a curved blade used for hollowing out the fellies, but this action resulted in damage
to the grain of the timber, and in consequence, the wood was weakened. To overcome this, a method of bending timber into a
circular form was invented in order that the whole rim of the wheel consists of not more than two pieces, which are covered
with a tyre in a single piece.
Using this construction method it is possible to ensure that the circumference of the wheel was equally strong everywhere, and
much more durable than wheels made in the usual form. From the hub radiated the wheel's spokes. Spokes were always of cleft, and
not sawn, oak as this produced a stronger spoke. Spokes were only finished and ready for use once they had been shaved, first with
a drawknife and then with a spokeshave. Shaving allowed the wheelwright to remove unnecessary weight whilst ensuring the spoke's
strength remained. They were driven into the hub with either a sledgehammer or the back of an axe, a process lasting about an hour.
In the 1920s, Jack Rice was carpenter, wheelwright, postman and lamplighter.